
REP fait appel aux compétences R&D de Parker Hannifin
03/10/2017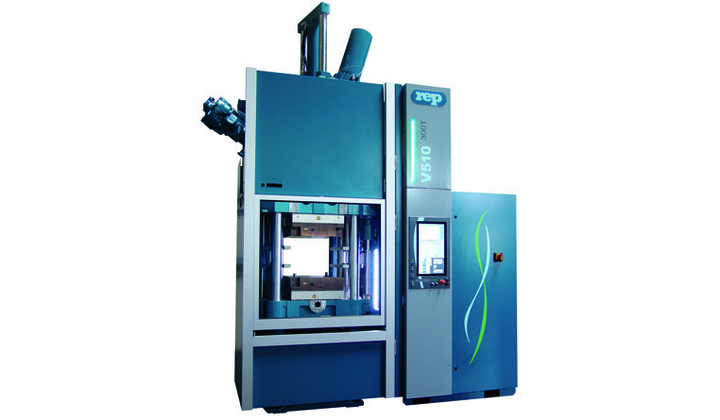
REP International, une société spécialisée dans la construction de presses à injecter, a fait appel à Parker Hannifin pour développer un système de servo motopompe immergée. Une technologie innovante qui a permis de réduire considérablement les consommations d’énergie.
Fournisseur de solutions pour l'industrie des caoutchoucs, thermoplastiques et autres polymères, REP International conçoit, fabrique et commercialise des presses à injecter verticales et horizontales de haute technologie pour le moulage du caoutchouc et du plastique.
Les clients de REP appartiennent à différents secteurs que sont l’automobile (60% du chiffre d’affaires), l’industrie et le BTP, le médical ou encore l’électroménager. « Dans le domaine du caoutchouc et des élastomères, nos clients sont confrontés à des efforts importants ; c’est pourquoi ils exigent de nos machines des niveaux maximum de robustesse et de longévité, précise Laurent Terrier, responsable du développement produit chez REP International.Certaines de nos presses sont installées depuis plus de quarante ans !Nous sommes toujours en mesure de fournir les pièces détachées et modifier les machines si le client le souhaite».
Les machines REP s’adressent à l’ensemble de la gamme d’élastomères existant sur le marché. A cette réputation de polyvalence s’ajoute celle de la fiabilité. Les raisons de cette robustesse : un savoir-faire reposant sur la maîtrise des régulations de vitesse et d’effort durant la phase d’injection afin de compenser la réaction de l’élastomère. Lors de cette étape déterminante du process, le caoutchouc est élastique et est de fait particulièrement soumis aux vibrations.
Mais les exigences de fiabilité et de simplicité d’utilisation ne suffisent plus. Désormais, les industriels, et ce quel que soit le secteur d’activité, ont en ligne de mire les économies d’énergie, pour des raisons de coûts bien sûr, mais aussi pour une dimension environnementale évidente. Au niveau des presses, l’objectif était à la fois de diminuer la consommation d’énergie électrique du groupe hydraulique et de réduire son encombrement.
Faire appel à Parker en tant que partenaire d’innovation
Recherchant un système innovant inexistant à cette époque sur le marché, REP fit appel à Parker Hannifin. « Nous travaillions déjà depuis plus de vingt ans avec Parker pour la fourniture de composants divers mais dans ce cas précisément, cette solution n’existait pas chez le fabricant, poursuit Laurent Terrier. C’est alors que nous avons commencé à collaborer étroitement avec les équipes de R&D de Parker pour définir nos besoins, effectuer de nombreux tests et mettre au point un système à la fois innovant, performant et pas trop onéreux pour enfin pouvoir le proposer en option sur l’ensemble de notre gamme de presses. Plus qu’un fabricant, Parker Hannifin s’est révélé être un partenaire d’innovation à part entière. Nous entretenons de très bonnes relations avec les équipes techniques et le responsable commercial – Vincent Sinot – qui s’est montré pleinement disponible et a tout mis en œuvre pour répondre à nos demandes».
Cette innovation – qui totalise trois ans de développement –, quelle est-elle ? Il s’agit plus précisément d’un système de servo motopompe immergée, lequel se compose de trois éléments : une pompe, un servomoteur et un variateur pour le contrôle. L’idée de départ était de remplacer les pompes auto-régulatrices par une solution capable d’adapter avec la plus grande précision un débit par rapport à un besoin réel : « le principe est le suivant : si j’adapte mon débit, j’adapte aussi ma vitesse », précise Vincent Sinot, responsable commercial Parker Hannifin pour la région Rhône-Alpes et chargé du suivi du projet avec REP International. Le principe général est d’utiliser la vitesse de rotation du moteur afin de contrôler le débit en sortie de pompe.
C’est sur ce principe fondamental que repose la technologie Drive Control Pump (DCP), une solution aujourd’hui disponible dans le catalogue Parker. Cette régulation du débit et de la pression par le contrôle de la vitesse et du couple du servomoteur, procure des avantages indéniables, à la fois en matière de réduction de consommation d’énergie mais aussi au niveau de la « simplicité » d’installation des composants hydrauliques. « En termes d’encombrement, la taille de la motopompe est réduite ; une performance car il a fallu tenir compte du système de commande (variateur) qui n’est pas négligeable, ajoute Laurent Terrier.Après ce choix, nous avons continué à travailler ensemble à la mise au point du système. Aujourd’hui, la solution est stabilisée. Elle est montée en option sur l’ensemble de nos machines depuis 2012. Des pistes d’optimisation sont en cours d’étude par Parker. Nous attendons ces nouvelles évolutions pour poursuivre les tests et aller encore plus loin dans notre démarche environnementale ».