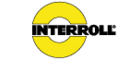
Le système de stockage dynamique d’Interroll retenu par Getrag Ford Transmissions
16/10/2014
Interroll vient d'installé un système de stockage dynamique dans l’usine de Getrag Ford Transmissions située à Liverpool permettant ainsi de centraliser et de stocker les composants conditionnés sur palettes plus à proximité des chaînes de production,
Avec près de 13 250 employés répartis sur 24 sites, Getrag est le plus grand fournisseur mondial indépendant de boîtes de vitesses et de systèmes de transmission pour les voitures de tourisme et les véhicules utilitaires légers.
L'ensemble de rayonnages dynamiques munis du système Pallet Flow d’Interroll qui a été installé, offre un stockage suivant le principe FIFO (premier entré, premier sorti) qui économise de la place et de l’énergie. Il compte au total 228 positions de palettes réparties dans des rayonnages de 4 palettes de profondeur, avec 3 étages de haut et 19 allées.
Neil Hodgkinson, ingénieur logistique travaillant pour Getrag Ford Transmissions, a dirigé ce projet d’amélioration du stockage des composants dans le cadre d’un projet plus large d’organisation au plus juste de la logistique, lequel vise à centraliser les opérations logistiques au sein de l’usine. Au cours de la discussion, il a confirmé le succès du projet en déclarant : « Le nouveau système Pallet Flow d’Interroll a été placé plus près de notre zone de production et il fournit un stockage cubique compact qui économise de la place tout en permettant de regrouper les produits identiques dans un seul couloir. En retour, cela simplifie la localisation et la préparation des commandes de composants afin de soutenir la production de 1 600 à 2 000 boîtes de vitesses par jour. »
En partant de produits palettisés et entreposés en bloc, Interroll a dû relever le défi qu’offrait la manutention d’un mélange de palettes en plastique et en bois, de tailles différentes ainsi que de configurations de base et de poids variés. Cela allait des euro-palettes de 800 mm x 1 200 mm aux palettes britanniques de 1 000 mm x 1 200 mm en passant par des palettes en plastique comptant 3 skis au niveau de la base ainsi que par les palettes conçues avec 9 pieds moulés et rehaussés en plastique. Le poids des diverses palettes variait de 600 à 1 000 kg. Il était donc essentiel pour Interroll d’identifier précisément les spécifications techniques correctes des modules dynamiques afin d’assurer un déplacement régulier, contrôler et fluide des palettes.
Afin de prévenir tout problème de fonctionnement et de garantir la longévité de l’installation en respectant un niveau de sécurité maximal, une sélection des palettes du client a été transférée au Centre d’Excellence d’Interroll pour le stockage dynamique situé à La-Roche-sur-Yon en France où des essais ont été effectués au sein du centre d’essai d’Interroll. Dans le but de fournir une solution optimale, Interroll a procédé à des tests sur des modules à rouleaux en conditions contrôlées, à température ambiante, en transportant les types et les charges de palettes spécifiques au client. Ces tests ont pris en compte l’inclinaison de la pente, la vitesse contrôlée de la descente, la séparation en ligne et le redémarrage des palettes arrêtées.
Après plusieurs phases d’essais, Interroll a pu valider la solution adéquate : des voies de stockage présentant chacune des rouleaux de 60 mm de diamètre au pas de 78 mm et équipée du nouveau système Safety Separator d’Interroll qui inclue la fonction Time Plus, laquelle assure la sécurité des opérateurs et améliore l’utilisation de la solution. Après avoir enlevé la première palette, du côté préparation de commandes, une temporisation de 20 secondes s’enclenche avant que la butée de séparation ne libère la palette suivante. Cela confère au cariste le temps nécessaire pour décharger la palette en toute sécurité avant que la seconde palette ne soit libérée. La pression des palettes suivantes ne s’applique alors pas sur son chariot élévateur. A grande hauteur, ce système de Safety Separator rend le travail de l’opérateur bien plus sûr et efficace.
Les régulateurs de vitesse d’Interroll maintiennent la palette à une vitesse constante de 0,3 m/s, quel que soit le poids de la palette. Dans le but de contrôler la vitesse des différentes palettes utilisées, une configuration spéciale a dû être adoptée, principalement dû à la présence de palettes en plastique. Chaque rouleau a été moleté en trois positions stratégiques en vue de créer une surface d’adhésion par friction et de contrôler la vitesse jusqu’à l’arrêt final. Cette solution a parfaitement fonctionné pour tous les types de palette.
Motivée par l’expérience positive du travail avec Interroll durant la phase de test et de développement d’une solution performante de stockage dynamique, l’entreprise Getrag Ford Transmissions a demandé à Interroll de travailler en étroite collaboration avec la société Planned Storage Systems qui avait été choisie pour l’intégration des modules dynamiques au sein du rayonnage.
Toutes les allées FIFO d’Interroll ont été équipées de rouleaux de 1 250 mm de long afin de parer à l’introduction éventuelle de palettes en bois de 1 200 x 1 200 mm dans le système à n’importe quel moment dans le futur. Dans les semaines suivant l’installation, cette précaution s’est déjà révélée on ne peut plus visionnaire puisque des palettes en bois de cette taille apparaissent maintenant dans la chaîne d’approvisionnement.
Parmi les spécifications du projet, la capacité portante requise était incluse, afin de pouvoir supporter les nouveaux rayonnages de stockage dynamique et étant donné que la surface de plancher choisie était carrelée, Getrag Ford a fait appel à des ingénieurs-conseils de PSA Design pour entreprendre une étude structurelle de la zone et prélever des carottes à des fins d’examen. Les tests d’écrasement des carottes ont prouvé que la zone carrelée ne présentait qu’un sixième de la résistance du sol plein et suite aux recommandations des ingénieurs, des plaques de charge dédiées ont été utilisées pour répartir la charge de chaque pied du rayonnage.
Getrag Ford Transmissions se dote du système de stockage dynamique d’Interroll |
|
Kettering, Royaume-Uni et Sant’Antonino, Suisse, le 16 octobre 2014. Interroll a récemment installé un système de stockage dynamique dans l’usine de Getrag Ford Transmissions située à Liverpool. Dans le cadre d’investissements importants effectués au sein de l’usine de Halewood Getrag Ford Transmissions, la décision a été prise de centraliser et de stocker les composants conditionnés sur palettes plus à proximité des chaînes de production, et ce, dans un ensemble de rayonnages munis du système Pallet Flow d’Interroll. Ce nouveau système Pallet Flow d’Interroll offre un stockage suivant le principe FIFO (premier entré, premier sorti) qui économise de la place et de l’énergie. Il compte au total 228 positions de palettes réparties dans des rayonnages de 4 palettes de profondeur, avec 3 étages de haut et 19 allées. |
|
Neil Hodgkinson, ingénieur logistique travaillant pour Getrag Ford Transmissions, a dirigé ce projet d’amélioration du stockage des composants dans le cadre d’un projet plus large d’organisation au plus juste de la logistique, lequel vise à centraliser les opérations logistiques au sein de l’usine. Au cours de la discussion, il a confirmé le succès du projet en déclarant : « Le nouveau système Pallet Flow d’Interroll a été placé plus près de notre zone de production et il fournit un stockage cubique compact qui économise de la place tout en permettant de regrouper les produits identiques dans un seul couloir. En retour, cela simplifie la localisation et la préparation des commandes de composants afin de soutenir la production de 1 600 à 2 000 boîtes de vitesses par jour. »
Avec près de 13 250 employés répartis sur 24 sites, Getrag est le plus grand fournisseur mondial indépendant de boîtes de vitesses et de systèmes de transmission pour les voitures de tourisme et les véhicules utilitaires légers.
La société Getrag Ford Transmissions a été créée en 2001 avec Ford Motor Company comme partenaire, Getrag assumant la responsabilité de la gestion opérationnelle des employés de six sites européens, lesquels produisent des boîtes de vitesses manuelles, automatiques et à double embrayage.
Depuis, ce modèle commercial performant a été élargi aux marchés asiatiques où l’organisation a agrandi ses usines de production qui emploient désormais 4 400 employés et produisent plus de 900 000 boîtes de vitesses par an.
Les modules du stockage dynamique d’Interroll ont fait leurs preuves sur le banc d’essai En partant de produits palettisés et entreposés en bloc, Interroll a dû relever le défi qu’offrait la manutention d’un mélange de palettes en plastique et en bois, de tailles différentes ainsi que de configurations de base et de poids variés. Cela allait des euro-palettes de 800 mm x 1 200 mm aux palettes britanniques de 1 000 mm x 1 200 mm en passant par des palettes en plastique comptant 3 skis au niveau de la base ainsi que par les palettes conçues avec 9 pieds moulés et rehaussés en plastique. Le poids des diverses palettes variait de 600 à 1 000 kg. Il était donc essentiel pour Interroll d’identifier précisément les spécifications techniques correctes des modules dynamiques afin d’assurer un déplacement régulier, contrôler et fluide des palettes.
Afin de prévenir tout problème de fonctionnement et de garantir la longévité de l’installation en respectant un niveau de sécurité maximal, une sélection des palettes du client a été transférée au Centre d’Excellence d’Interroll pour le stockage dynamique situé à La-Roche-sur-Yon en France où des essais ont été effectués au sein du centre d’essai d’Interroll. Dans le but de fournir une solution optimale, Interroll a procédé à des tests sur des modules à rouleaux en conditions contrôlées, à température ambiante, en transportant les types et les charges de palettes spécifiques au client. Ces tests ont pris en compte l’inclinaison de la pente, la vitesse contrôlée de la descente, la séparation en ligne et le redémarrage des palettes arrêtées.
Après plusieurs phases d’essais, Interroll a pu valider la solution adéquate : des voies de stockage présentant chacune des rouleaux de 60 mm de diamètre au pas de 78 mm et équipée du nouveau système Safety Separator d’Interroll qui inclue la fonction Time Plus, laquelle assure la sécurité des opérateurs et améliore l’utilisation de la solution. Après avoir enlevé la première palette, du côté préparation de commandes, une temporisation de 20 secondes s’enclenche avant que la butée de séparation ne libère la palette suivante. Cela confère au cariste le temps nécessaire pour décharger la palette en toute sécurité avant que la seconde palette ne soit libérée. La pression des palettes suivantes ne s’applique alors pas sur son chariot élévateur. A grande hauteur, ce système de Safety Separator rend le travail de l’opérateur bien plus sûr et efficace.
Les régulateurs de vitesse d’Interroll maintiennent la palette à une vitesse constante de 0,3 m/s, quel que soit le poids de la palette. Dans le but de contrôler la vitesse des différentes palettes utilisées, une configuration spéciale a dû être adoptée, principalement dû à la présence de palettes en plastique. Chaque rouleau a été moleté en trois positions stratégiques en vue de créer une surface d’adhésion par friction et de contrôler la vitesse jusqu’à l’arrêt final. Cette solution a parfaitement fonctionné pour tous les types de palette.
L’expérience positive triomphe Motivée par l’expérience positive du travail avec Interroll durant la phase de test et de développement d’une solution performante de stockage dynamique, l’entreprise Getrag Ford Transmissions a demandé à Interroll de travailler en étroite collaboration avec la société Planned Storage Systems qui avait été choisie pour l’intégration des modules dynamiques au sein du rayonnage.
Présente à l’installation et à la mise en service en mars 2014, Interroll a entrepris une série de formations sur place afin de transmettre les instructions nécessaires à tous les opérateurs pertinents de Getrag Ford Transmissions et de leur fournir un cahier des charges concernant les divers composants des modules. Ces sessions de formation concernaient le fonctionnement des composants clés, les questions de sécurité, les techniques de chargement dont le positionnement des mâts de chariot élévateur à 4% et du déchargement avec le séparateur Time Plus d’Interroll, etc.
Toutes les allées FIFO d’Interroll ont été équipées de rouleaux de 1 250 mm de long afin de parer à l’introduction éventuelle de palettes en bois de 1 200 x 1 200 mm dans le système à n’importe quel moment dans le futur. Dans les semaines suivant l’installation, cette précaution s’est déjà révélée on ne peut plus visionnaire puisque des palettes en bois de cette taille apparaissent maintenant dans la chaîne d’approvisionnement.
Parmi les spécifications du projet, la capacité portante requise était incluse, afin de pouvoir supporter les nouveaux rayonnages de stockage dynamique et étant donné que la surface de plancher choisie était carrelée, Getrag Ford a fait appel à des ingénieurs-conseils de PSA Design pour entreprendre une étude structurelle de la zone et prélever des carottes à des fins d’examen. Les tests d’écrasement des carottes ont prouvé que la zone carrelée ne présentait qu’un sixième de la résistance du sol plein et suite aux recommandations des ingénieurs, des plaques de charge dédiées ont été utilisées pour répartir la charge de chaque pied du rayonnage.
Neil Hodgkinson poursuit : « De nombreux avantages supplémentaires peuvent être attribués à ce nouveau système, tel que le principe FIFO qui permet d’obtenir une rotation adéquate des stocks et de s’assurer que les premières livraisons soient toujours utilisées en premier. Étant donné que cette industrie se développe très vite en présentant régulièrement des conceptions et des designs innovants, il est important que nous utilisions toujours nos stocks en suivant le principe « premier entré, premier parti » afin de s’assurer que des composants ne soient pas remplacés et que les stocks ne deviennent pas redondants ou soient considérés comme des déchets et des rebuts. De plus, les mouvements des chariots élévateurs sont considérablement réduits étant donné que les rayonnages sont confinés à des domaines d’opération clairement délimités, ce qui respecte les exigences très strictes de sécurité telles qu’elles sont en vigueur au sein des usines de Getrag Ford Transmissions.
Au début du projet de centralisation des composants entrants, le concept de stockage dynamique de palettes constituait un projet intéressant mais il incluait aussi un certain nombre de défis et nécessitait donc l’appui d’experts. Avec de nombreuses variantes de palettes au niveau de la construction, de la taille, des matériaux ou du poids, nous avons adressé nos nombreuses questions au Centre d’excellence d’Interroll pour le stockage dynamique situé en France et nous en sommes revenus avec la bonne solution !
L’installation nous a donné entière satisfaction et je peux confirmer que le feedback de notre équipe logistique est très encourageant puisqu’il la considère comme une évolution positive. »
Contact en France Julien Sanquer Interroll France Service communication ZI de Kerannou BP 34 │29250 Saint Pol De Léon │ France +33 2 98 24 69 09
Contact en Suisse Petra Müller Interroll (Schweiz) AG Responsable des relations publiques et des Relations investisseurs Via Gorelle 3 │ 6592 Sant'Antonino │ Suisse +41 91 850 25 21 |
|
|
|
Interroll Le groupe Interroll est l'un des spécialistes mondiaux leaders de produits et de prestations de services clés haut de gamme dans le domaine de l’intralogistique. La société fournit plus de 23.000 clients dans le monde et propose le plus vaste éventail de produits, répartis selon quatre groupes : les rouleaux de manutention, les moteurs et entraînements pour convoyeurs, les modules de transitique et de trieurs haute cadence ainsi que les systèmes de stockage dynamique pour cartons et palettes. Les produits Interroll sont utilisés dans la logistique postale et les services de messagerie, la logistique aéroportuaire, l’industrie agroalimentaire, sans oublier la distribution et autres industries plus générales. Parmi ses clients figurent des marques de renommée internationale, telles qu'Amazon, Bosch, Coca-Cola, Coop, DHL, FedEx, Peugeot, PepsiCo, Procter & Gamble, Siemens, Walmart ou Yamaha. Interroll est engagée dans des projets de recherche à l'échelle internationale dans le secteur de l'efficacité logistique et soutient de manière active des associations industrielles en matière de développement de normes. Basé à Sant’Antonino, Suisse, Interroll dispose d'un réseau mondial de 31 filiales et de 1.800 collaborateurs. Fondée en 1959, la société est, depuis 1997, cotée à la SIX Swiss Exchange et représentée dans l'indice SPI.
Getrag Getrag est l’un des plus grands fournisseurs de systèmes de transmission au monde avec près de 13 250 employés répartis sur 24 sites. Le siège du Groupe se trouve à Untergruppenbach, en Allemagne. L’entreprise développe et produit des solutions de transmission pour l’industrie automobile. Getrag possède un large assortiment de produits comptant des boîtes de vitesses manuelles et automatiques ainsi qu’à double embrayage. La société propose aussi diverses options de transmissions hybrides et électriques. En 2013, son chiffre d’affaires s’élevait à 3,2 milliards d’euros.
|
Autres actualités Interroll
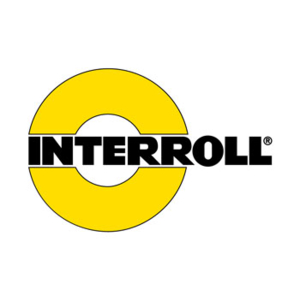
Interroll expose au salon CFIA 2017
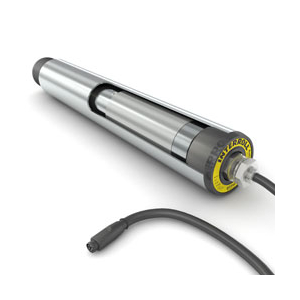
Rouleau moteur EC 310
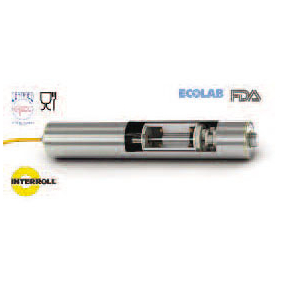
Tambour Moteur brushless
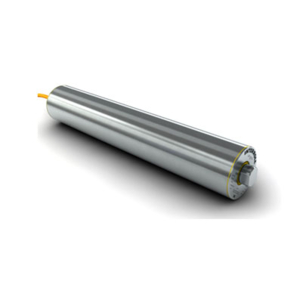