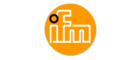
Les capteurs IO-Link d'ifm electronic équipe les machines-outils du constructeur Allemand Starrag Technology
28/06/2018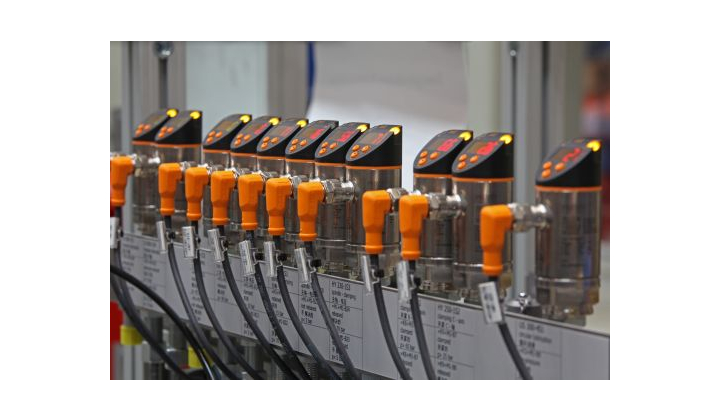
Starrag Technology GmbH a opté pour les capteurs de fluides IO-Link d'ifm electronic. Ces capteurs, avec leurs interfaces économiques et fiables, fournissent plus d'informations sur le process, ce qui permet de mieux l’évaluer et l’optimiser
Transformation numérique avec IO-Link
Lors du passage vers l'industrie 4.0, il faut, entre autres, générer une représentation numérique de l’installation afin d’analyser et d'optimiser les processus. Les nombreux capteurs déjà installés pour le contrôle des machines servent de sources d'informations. Grâce à la technologie IO-Link, ces capteurs fournissent bien plus de données que des simples signaux de commutation TOR ou des valeurs analogiques.
La machine d'usinage portique de la série FOGS de la Starrag Technology GmbH fait partie des machines ainsi équipées qui sont utilisées dans la construction de machines, dans l'industrie aéronautique ou dans l'industrie automobile. Dans ce dernier secteur, elles sont par exemple utilisées dans la fabrication d'outils de presse pour la production de carrosseries (au niveau des éléments d'habillage). L'installation visible sur la photo sert dans l'industrie aéronautique à usiner des éléments du train d’atterrissage, plus précisément : les pieds d'atterrissage.
Pour ces machines-outils complexes, la surveillance de tous les fluides et états (par ex. réfrigérants et lubrifiants, l'hydraulique, la température de la machine) à l'aide de capteurs est essentielle. Dans un process de fabrication entièrement automatisé, l'utilisation optimale des outils n'est possible que si les températures des fluides, les valeurs de pression et les débits ne dépassent pas les très faibles tolérances permises.
Capteurs avec interface TOR
IO-Link est une interface numérique fiable basée sur des signaux à une tension de 24 V pour une communication bidirectionnelle avec le système de commande via la ligne de capteurs normale, comme alternative aux signaux de commutation. Les capteurs transmettent, via IO-Link, des valeurs mesurées et des informations de diagnostic numériques au maître IO-Link (par ex. un module E/S, une passerelle ou une API équipée de ports IO-Link). Leur raccordement se fait par des connecteurs M12 standards. Les câbles blindés ainsi que les mises à la terre associées ne sont plus nécessaires.
Paramétrage des capteurs à distance
Un gros avantage d'IO-Link est la possibilité de charger toutes les données de paramétrage nécessaires sur le capteur via le câble de raccordement IO-Link. Les données de paramétrage du capteur (par ex. seuils de commutation, hystérésis de commutation, couleur de l'affichage) peuvent être transmises du système de commande vers le capteur IO-Link soit une seule fois, au moment de la mise en service, soit en fonction des différentes situations pendant le fonctionnement. Les avantages pour le client : pendant la phase de mise en service d'une machine, les paramètres du capteur précédemment configurés peuvent être transmis au capteur rapidement, facilement et avec une grande fiabilité. Pendant le processus d'usinage (par ex. en cas de petits batchs), différents jeux de paramètres pour différents produits peuvent être appliqués individuellement au capteur si nécessaire grâce à la technologie IO-Link. De plus, grâce au paramétrage via le système de commande, des optimisations ultérieures des process peuvent être facilement effectuées via IO-Link et par télémaintenance. Cela démontre qu’IO-Link est une technologie de base pour les applications de l’Industrie 4.0.
Double sauvegarde des données
Allant de pair avec le paramétrage du capteur via le système de commande, IO-Link offre à partir de la version 1.1 un double stockage automatisé des données de paramétrage du capteur : et dans l'appareil et dans le maître IO-Link.
Les capteurs mal paramétrés font donc partie du passé. Le remplacement des capteurs ne devient alors plus qu'un simple montage mécanique. Le client peut lui-même effectuer le remplacement. Le personnel de maintenance n'a pas besoin de compétences en paramétrage de capteurs car ce dernier s'effectue automatiquement en arrière-plan. Les interventions dues aux pannes peuvent alors s'effectuer de manière nettement plus rapide et fiable. Cela réduit les coûts.
Transmission numérique des valeurs mesurées sans erreur
Jusqu'à présent, les signaux analogiques des capteurs sont numérisés via un convertisseur A/N et mis à l'échelle dans l'API. Ceci peut entraîner l’inexactitude de la valeur mesurée.
En revanche, IO-Link transmet numériquement les valeurs mesurées du capteur au système de commande. Il n'y a plus de transmission défectueuse de signaux analogiques et leur conversion est devenue superflue. Les valeurs mesurées transmises numériquement peuvent directement être visualisées au poste de commande, et la valeur transmise correspond toujours exactement à la valeur mesurée. Il n'y a plus d’écarts entre l'affichage sur site et la valeur déterminée par un signal analogique dans l'API. Avec IO-Link, d'éventuelles influences parasites sur le signal analogique, provoquées par ex. par des champs électromagnétiques, font également partie du passé.
Deux valeurs mesurées - un seul capteur
Les capteurs de process modernes d'ifm fournissent souvent bien plus qu'une seule valeur mesurée, comme le confirme Dietmar Wallenstein : "Souvent, un capteur traite plus qu'une seule valeur physique. Ainsi, outre le débit ou la pression, il est par exemple également possible de lire la température du fluide via IO-Link ce qui, auparavant, n'était possible qu'en utilisant deux capteurs." Cela représente une économie d'argent au niveau du matériel, du câblage et du montage, car il n'y a plus besoin que d'un seul capteur au lieu de deux ce qui, par conséquent, ne nécessite plus qu'un seul emplacement pour le montage.
Données de diagnostic
En plus des données process, le capteur IO-Link peut également fournir des données de diagnostic par rapport à l'état de l'appareil lui-même. Exemple : le capteur de niveau détecte des dépôts critiques qu'il indique ensuite au système de commande. Les détecteurs optoélectroniques détectent eux-mêmes des salissures au niveau de la lentille et les signalent automatiquement. Les capteurs de pression sauvegardent des chutes de pression minimales et des pics de pression maximales survenant dans le process et totalisent le nombre de dépassements vers le haut ou vers le bas - une fonctionnalité supplémentaire qui apporte un soutien décisif à l'utilisateur au niveau de la maintenance préventive conditionnelle. Ces informations d'état étendues réduisent les temps d'arrêt coûteux tout en augmentant la sécurité du process.
Autres actualités ifm electronic
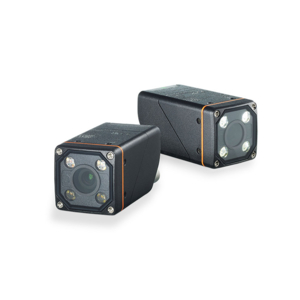
Lecteur multicode O2I avec IO-Link
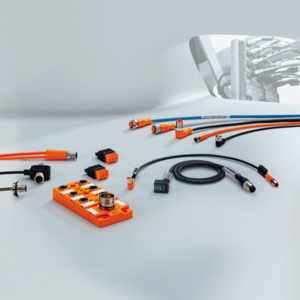
Connecteurs industriels Ecolink
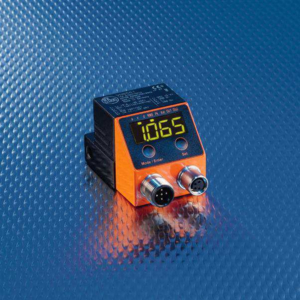
Capteur de vibrations VNB001
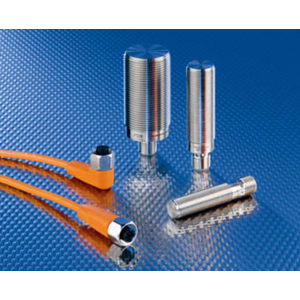
Détecteurs inductifs tout métal
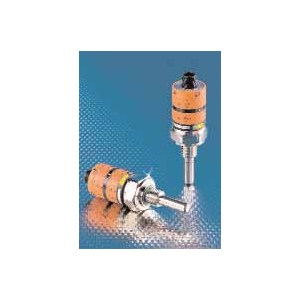